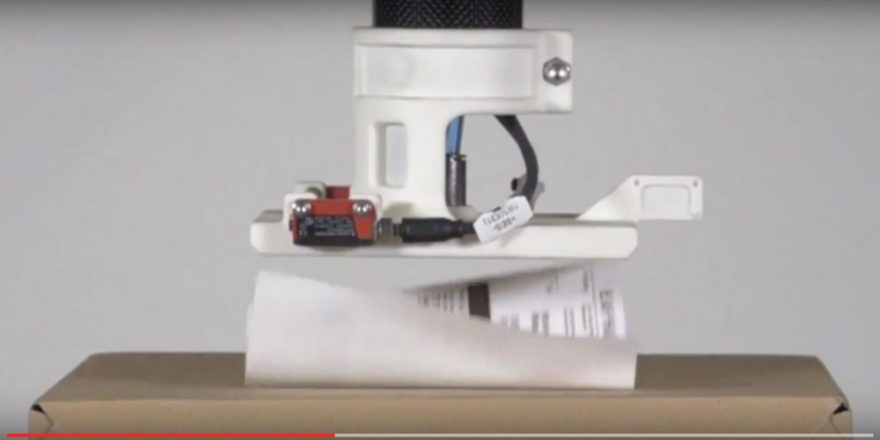
Variably printed labels can be applied to a product or packaging using a variety of methods. Most impressive is certainly the “blow” method of labeling, which we would like to introduce to you today.
The most common is the design with an additional postmark – in our language use “Tamp”. In this “Tamp Blow” variant, the label is first supplemented by a printer with the variable text or barcode information. It is then pushed onto a punch in which a vacuum prevails. The vacuum is applied to the stamp. With the adhesive side down, wait for the part to be labeled.
Tamp Blow
Once it is within range, the punch drives down. The vacuum switches off and at the same time an overpressure is generated in the punch. The label literally shoots away from the stamp plate and ends up in the right place. If the product and glue match properly (the expert is required here), then it clings immediately and it is not necessary to press or brush it.
The following slowdown and the introductory picture for our post show that during the course of some amazing things happen with the label.
It does not fly uniformly towards the product, but is very vaulted. In other applications, parts of the label even bounce off the surface of the product, but then finally “calm down” and surrender to their destiny.
Wipe On
As an alternative to the “Tamp Blow” process, the “Wipe On” method can also be used. During the printing of the label, the label is then applied to the article. The two speeds of the printing process and of the conveying process are, of course, to be synchronized, so that no wrinkles arise during the gluing.
The most important advantages of the Tamp Blow process are obvious:
- The printing of the label and the gluing on it do not have to take place synchronously with the product movement. The label waits until the beginning of the labeling process.
- The product can move faster than the printer can print.
- Also the application of the label to a fast moving product works.
- The label can also be inflated.
- A precise alignment of the product with the labeling is not necessary.
- It is also possible to label products of different heights. A certain distance corresponds to the movement of the stamping, the rest of the jaw bridges the targeted air jolt.
The following points must be observed when using the Wipe-On method:
- The product must not run faster than the printer prints. If the package should stop, the printer must also temporarily stop printing.
- Positive: The label can also be pressed onto the product surface with a roller or a brush. This also makes it possible to label difficult product surfaces without bubbles.
The right holes in the right place
It is very important that the size, quantity and arrangement of the holes in the die plate are precisely adapted to the particular application. There must always be a sufficiently high vacuum to keep the label in place during labeling. The label must therefore properly cover the suction holes. And yet it is necessary to direct the subsequently generated overpressure in the correct sequence to the correct blowing openings. The interior of such a postmark can therefore be quite complex. More and more often, we use 3D-printed parts in the production machines because they can be more flexibly adapted to the respective requirements.
The interplay between label, label adhesive, stamp during the two processes of printing and applying is not trivial. We can build on decades of experience here.
Further information on labels and labeling systems can be found on our website.