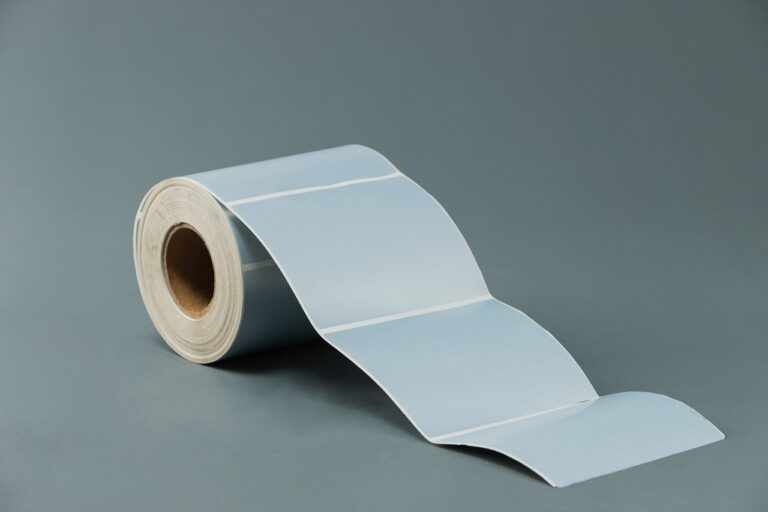
You’ve just acquired a new label printer for your shipping department, one that’s perfect for producing labels with barcodes and high-quality images. But hold on a second – it offers both thermal-transfer and direct thermal printing modes. What does that mean for your labeling needs? In this guide, we’ll delve into the differences between these two printing technologies, helping you make an informed decision that suits your requirements.
Exploring the Depths of Label Printing Technology
When you send label content to your printer, it activates the print head, which heats up specific areas to form your desired image. These areas consist of microscopic dots that collectively create words, images, and more. Printers are usually rated in dots per inch (dpi), commonly at 203, 300, or 600 dpi. However, the real divergence begins here:
Thermal-Transfer Printing
Thermal transfer printing operates by heating the print head, which then transfers its heat to a ribbon made of wax, wax/resin, or pure resin. This ribbon melts selectively to craft the image, subsequently transferring it onto the thermal print label as it passes through the printer. The ribbon ink solidifies on the thermal print label, producing a sharp, clear representation of your information.
Thermal-transfer labels consist of coated paper or film with adhesive backing to ensure secure adherence to your product or package.
Direct Thermal Printing
Direct thermal print label printing takes a different route. It involves loading direct thermal print label, which don’t require a ribbon. Instead, the label material itself is coated with a special top coat that’s heat-sensitive. When you initiate a print job on a direct thermal printer, the print head imparts heat to specific areas of the thermal print label, causing those areas to darken, thus creating your desired information.
Choosing the Right Path for Your Needs
Now, let’s address the question on every label printer user’s mind: which method should you choose?
Thermal-Transfer Printing: Durability and Clarity
Thermal-transfer printing is exceptionally well-suited for a wide range of applications where the utmost durability and impeccable legibility of labels are paramount. What sets this method apart is its ability to adapt to varying levels of durability, contingent upon the specific ribbon utilized. The choice between wax, wax/resin, or pure resin ribbons allows for customization, making it possible to produce thermal print labels that excel in demanding environments, from extreme temperatures to exposure to liquids and abrasion.
Consequently, thermal-transfer printing is an ideal choice for crafting archival-quality labels that are engineered to endure the harshest conditions. This method shines in various applications, including but not limited to wristbands, product identification, asset tagging, and more. Furthermore, when it comes to printed barcodes, thermal-transfer labels consistently offer a level of superiority, ensuring their resilience and resistance to fading, setting them apart from their direct thermal print label counterparts.
Direct Thermal Printing: Cost-Efficiency and Quick Use
Direct thermal printing, in contrast, presents an attractive option for businesses seeking immediate cost savings, as it eliminates the need for a ribbon, streamlining operational expenses. Its true strengths shine in scenarios where high-volume variable information labels are the order of the day, such as the rapid generation of address labels. This method also finds common use in the creation of temporary labels, one-day wristbands, shipping labels, and pick tickets, making it a favored choice for situations requiring quick, efficient labeling.
However, it’s important to note that direct thermal print label have their limitations. Over time, images on these thermal print labels may gradually fade when exposed to elevated temperatures, intense illumination, or challenging environmental conditions. Due to this susceptibility, they are not recommended for long-term identification purposes, where permanence and longevity are essential. Consequently, while direct thermal printing offers immediate cost benefits and rapid label production, users should weigh these advantages against the potential for fading in extended use cases.
Conclusion
Tailoring Your Choice The key to selecting the right printing method is a careful analysis of your specific needs. If you’re primarily generating shipping labels meant to last a few days, direct thermal print labels are a cost-effective choice. However, for labels that demand longevity and impeccable barcode clarity, thermal-transfer labels are the way to go.
For more information or to explore pricing on thermal-transfer label printers, ribbons, and labels, visit our store. We’re here to help you make the best choice for your thermal print label requirements.