EasyGo! InventoryHealthCare
Summary
EasyGo! InventoryHealthCare transforms your handheld into a stocktaking device for inventory management at your hospital or pharmacy. Especially designed for healthcare environments, use this application at your Hospital or Health Care centres to easily control your stock, such as medicines, equipment or other inventory. Next to the possibility to capture a zone, the location, and a quantity this applications allows as well for adding to each stock item healthcare specific data-fields such as batch and expiry dates. When stocktaking is complete, the data is uploaded to your host system for management reports and further processing.
Description
EasyGo! InventoryHealthCare application allows inventory management of any type of stock, with or without barcodes labels in your Healthcare environment. Capture the barcode of each the stock item, or in case there is no barcode available simply key in the product id. Add the quantity to each item and most importantly register the batch and/or lot numbers including the expiration dates.
Optionally you can ask the operator to identify the zone and location for easy product location tracking. It’s that easy!
EasyGo! InventoryHealthCare also allows the operator to check and edit previous inputs or to amend an error. When the inventory is done, the data is ready to be uploaded, via cradle or WiFi, to the host.
EasyGo! InventoryHealthCare workflow is fully customisable. The operator is prompted to provide zone, location, item, quantity, batch, expiry date, as necessary, all set according to the end-user’s inventory requirements. The workflow can be set up to loop on item and quantity until the inventory in that location is completed, or the operator can be required to re-enter the location for each item.
There is almost always a fit to each way of conducting inventories.
Languages
English
Spanish
Adobe Reader is required to open and view PDF files. This can be downloaded free from adobe.com.
Available Documents
SATO MBi Series
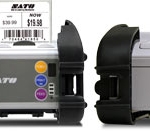
For fast, flawless barcode label printing to go, look no further than SATO’s MB2i and MB4i series of printers.
View ProductBasic Fast Inspector
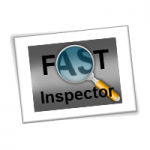
Summary
Inspection program is ideal for fixed assets or high-value items – such as automobiles, construction equipment or plant maintenance and tooling equipment.
View ProductAlpha Quadro Label Applicator
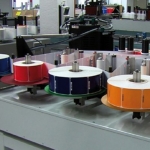
The right label at the right time
View ProductMarkoprint Integra One ip LX
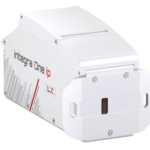
Unleash the Power of Proven Washdown Technology (IP Protection) for Seamless Performance in Complex and Demanding Applications. Experience High-Speed Printing and Effortless Operation with Up to 10 mm Print Distance. Discover Impressive Innovations, including a Patented Mechanism for Secure Ink/Printhead Unit Hold, Setting a New Standard in Printing Excellence.
View Product